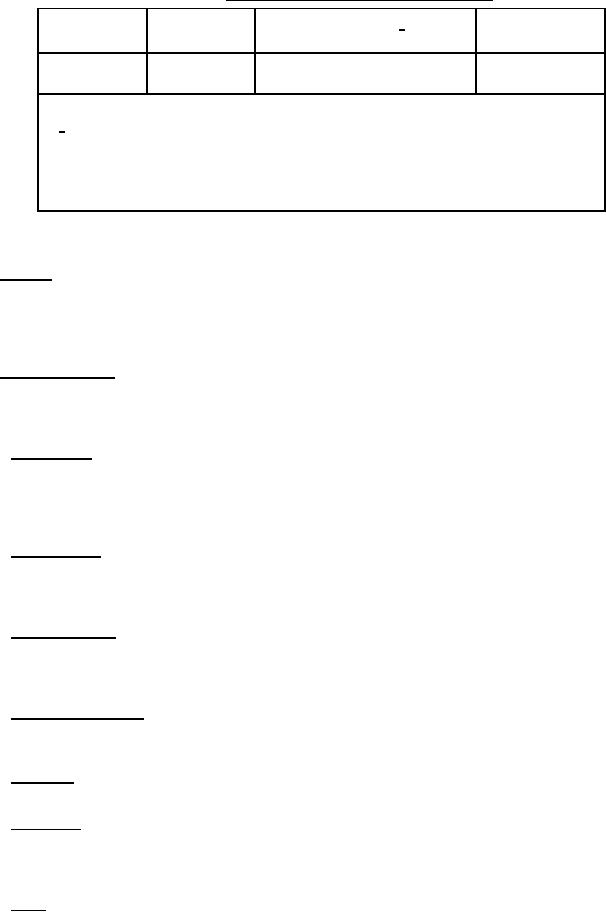
A-A-59001A(SH)
TABLE IV. Batterboard plank size and estimated weight.
Plank Estimated
Actual Size 1/
Panel Type
Nominal Size
Weight
7½ in × 189½ in × 3½ in
129.3 lb
Plank
8 in × 190 in
(190 mm × 4813 mm × 89 mm)
(58.6 kg)
FOOTNOTES:
1/
Planks are to be manufactured to tolerances shown in the manufacturing detail on
the fabrication drawings.
NOTES:
1.
Plank weights shown in tables are estimated. Actual panel weights may vary.
3. SALIENT CHARACTERISTICS.
3.1 Material. Synthetic batterboard panels shall consist of UHMWPE facing the well deck and shall be backed up
by an energy absorbing elastomer material. The UHMWPE material shall use a base virgin resin made in
accordance with ASTM D4020 and have a nominal molecular weight of 3.1 by 106 or greater. The UHMWPE and
elastomer materials shall be modified using additives and fillers as necessary to achieve the required properties
specified herein.
3.2 Material properties. The synthetic batterboard material(s) shall meet all of the requirements specified herein
when tested over a normal operating temperature range of -20 to +125 °F (-28.9 to +51.7 °C). The UHMWPE
surface facing into the well deck shall also be capable of withstanding brief excursions, not to exceed 2.0 minutes, at
a surface temperature of 220 °F (104.4 °C). Where applicable, test specimens shall be the full panel thickness.
3.2.1 Flame spread. The test specimens shall be prepared and tested in accordance with ASTM E162 and shall not
exceed a 25 ls (flame spread index) value. The test specimens shall be placed in the test fixture so that the impact
surface faces the flame source. The test specimen shall exhibit no dripping or puddling during the test and shall be
self-extinguishing after the flame source has been removed. Surface coatings or supplementary materials such as
long strand fiberglass shall not be used to retard burning of the synthetic batterboard panel.
3.2.2 Smoke density. The test specimen shall be evaluated to determine the relative amount of smoke produced by
burning or decomposition in accordance with ASTM E662. The test specimens shall be placed in the test fixture so
that the impact surface faces the flame source. The smoke generated during the flaming and nonflaming modes shall
not exceed 450 Dm (maximum specific optical density).
3.2.3 Impact resistance. UHMWPE test specimens shall be prepared and tested as described in ASTM D256,
Method A (except that the Izod specimens shall be unnotched). These unnotched test specimens shall be capable of
absorbing an Izod condition of 45 inch-pounds/inch (202 Joules/meter). No breakage or cracking of the test
specimen is permitted under any circumstances.
3.2.4 Coefficient of friction. The test specimen shall be prepared and tested in accordance with ASTM D1894. The
dynamic coefficient of friction of the UHMWPE surface facing into the well deck shall not exceed a 0.2 value
against steel (dry).
3.2.5 Resilience. The test specimen shall be prepared and tested in accordance with ASTM D2632. The energy
absorbing elastomer shall be formulated so that the resilience does not exceed a 25 percent rebound value.
3.2.6 Paintability. The low-coefficient of friction slippery surface facing into the well deck of the batterboard
panels or planks shall be capable of being painted for marking and coding. Paints meeting the requirements of the
Master Painters Institute, MPI #9, Alkyd, Exterior, (MPI Gloss Level 6) and MPI # 94, Alkyd, Exterior, Semi-Gloss,
(MPI Gloss Level 5) shall be used to ensure compliance.
3.2.7 Color. The color of the UHWMPE material shall be black unless otherwise specified (see 7.1).
6
For Parts Inquires call Parts Hangar, Inc (727) 493-0744
© Copyright 2015 Integrated Publishing, Inc.
A Service Disabled Veteran Owned Small Business